Quality control in construction significantly impacts client business operations after project completion. Therefore, proper management is essential to ensure quality at each stage of the project. This guide explores fundamental concepts and practical implementation of construction quality control from the client’s perspective.
What is Construction Quality Control?
Construction quality control (QC) encompasses activities designed to meet planned quality requirements. ISO 9001:2015 defines construction quality control as “processes necessary to deliver outcomes that meet requirements and applicable specifications.”
Construction quality control involves implementing a comprehensive PDCA (Plan-Do-Check-Act) cycle throughout the project, from clarifying quality requirements to developing QC plans, conducting regular inspections, maintaining records, and continuous improvement activities.
During the construction phase, key QC activities include:
- Material receiving inspection and quality verification
- Daily construction status checks
- Measurement and documentation of completed work
- Quality record creation and management
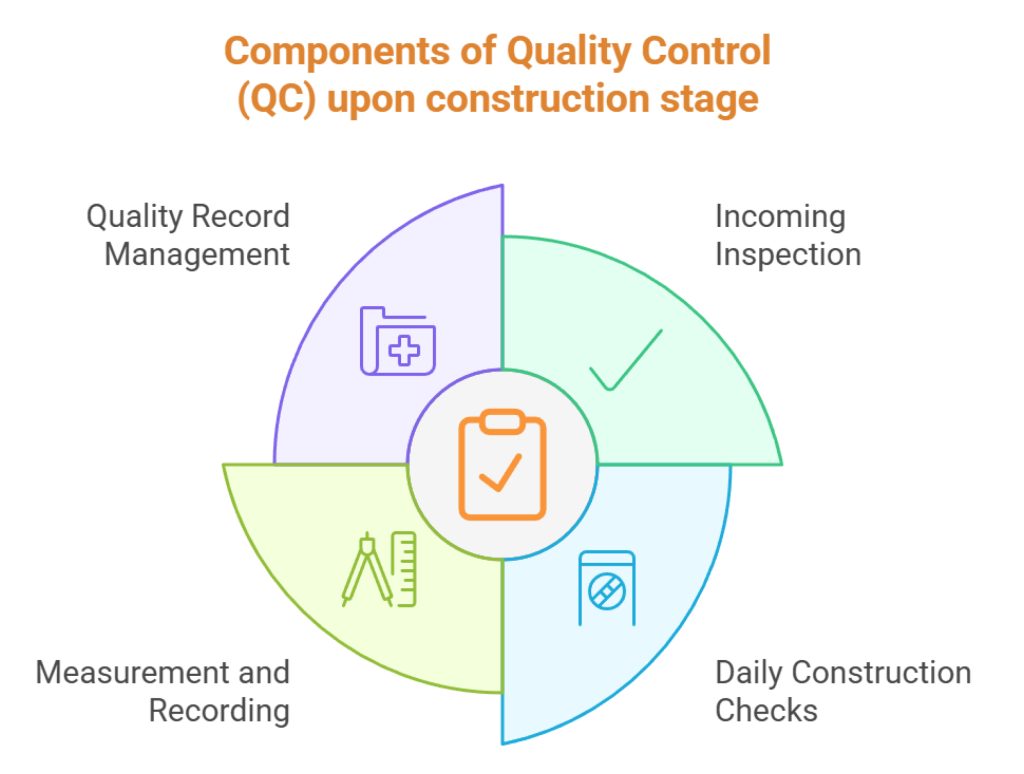
Understanding QC vs. QA in Construction
Achieving consistent quality requires integrating QC with another essential approach: Quality Assurance (QA).
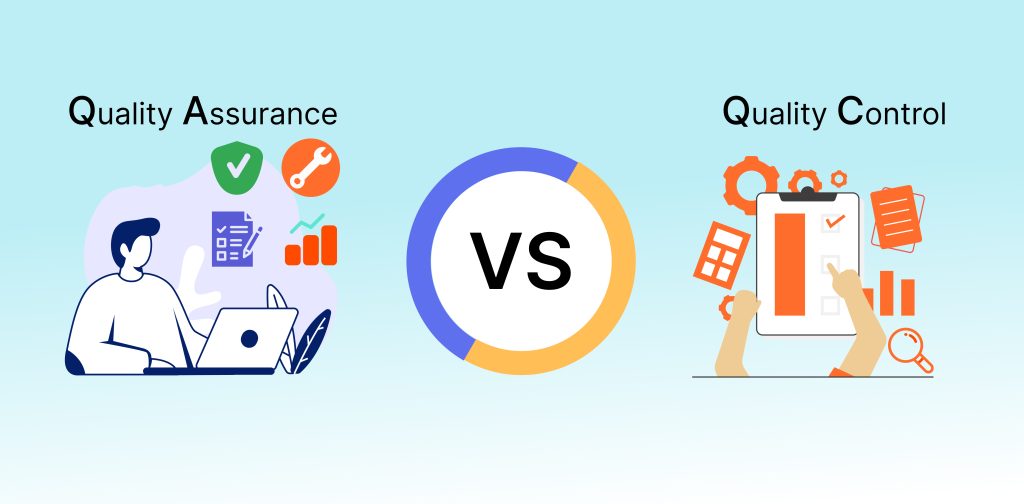
What is Quality Assurance?
Quality Assurance (QA) aims to establish appropriate quality systems. It covers a wide range of activities, from establishing and operating QC systems to implementing education and training programs. QA provides a systematic approach to maintaining consistent quality standards throughout the entire project. Key activities include:
- Developing and operating quality management systems
- Setting and documenting quality standards
- Implementing education and training programs
- Conducting regular quality audits
- Creating project quality plans
- Developing Inspection and Testing Plans (ITP)
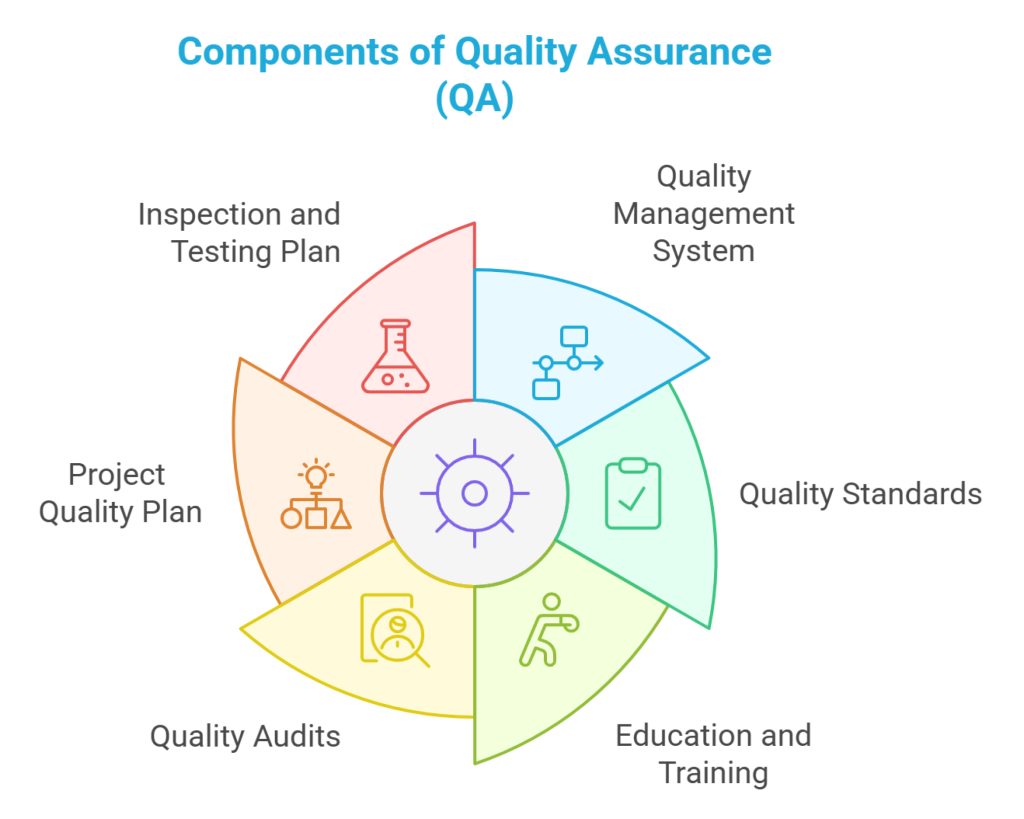
QA provides systematic oversight while QC handles specific verification tasks, creating a complementary relationship.
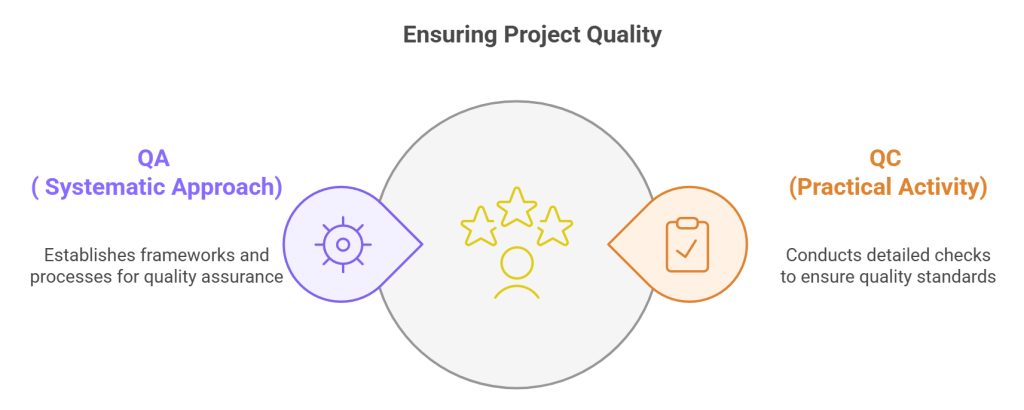
The Client’s Role
Clients play a crucial role, particularly in QA.
First, clients must clearly define what they aim to achieve in the project and share this vision with all stakeholders.
Next, it’s important to establish measurable QC systems, which involves organizing QC workshops, clearly defining responsibilities, and visualizing processes through diagrams.
Clients should also oversee all activities and promote necessary improvements to maintain the QA PDCA cycle effectively.
8 Essential Construction Quality Control Strategies
1. Clear Quality Requirements
Defining specific quality requirements at project initiation is crucial. At this stage, you need to identify detailed requirements beyond basic legal and industry standards that are specific to the project. For example, setting concrete numerical targets such as concrete strength or floor flatness can enhance the effectiveness of quality control.
Additionally, when establishing quality requirements, it’s important to consider the entire lifecycle of the building. Quality requirements should account for not only construction quality but also maintenance management and potential future renovations. This comprehensive approach helps ensure the building’s long-term value.
2. QC Plan Evaluation
QC plans provide specific measures to achieve the required quality. When evaluating these plans, pay particular attention to the following points:
- QC system appropriateness
- Inspection and testing method validity
- Record keeping procedures
- Non-conformance management processes
When conducting evaluations, don’t just verify the content; consider feasibility and efficiency as essential criteria. It’s important to carefully examine whether the plan will be effective under actual site conditions.
For more detailed information about feasibility study in construction projects, please refer to the following articles:
3. Thorough On-site Quality Verification
Conduct consistent quality checks following the QC plan. Daily quality verification activities, including pre-work condition checks and progress monitoring, are essential.
Maintain proper documentation with objective records like photographs and measurement data for future quality certification and issue resolution.
4. Quality Visualization
Visualize ongoing conditions to facilitate information sharing and early problem detection. Modern digital QC tools, including tablet-based inspections and cloud systems for information sharing, are increasingly common.
When non-conformances with QC plans are discovered, issue Non-Conformance Reports (NCR) for corrective action, documenting details for future prevention.
5. Non-conformance Management
When quality non-conformances are discovered, prompt action is required to prevent problems from escalating. Non-conformance management refers to a series of processes from problem identification through corrective action implementation and effectiveness verification. Rather than simply fixing issues, it’s essential to analyze root causes and develop preventive measures.
Furthermore, extending identified non-conformances to similar processes and other sites can help improve quality levels across the entire project. This approach enables raising overall project quality standards.
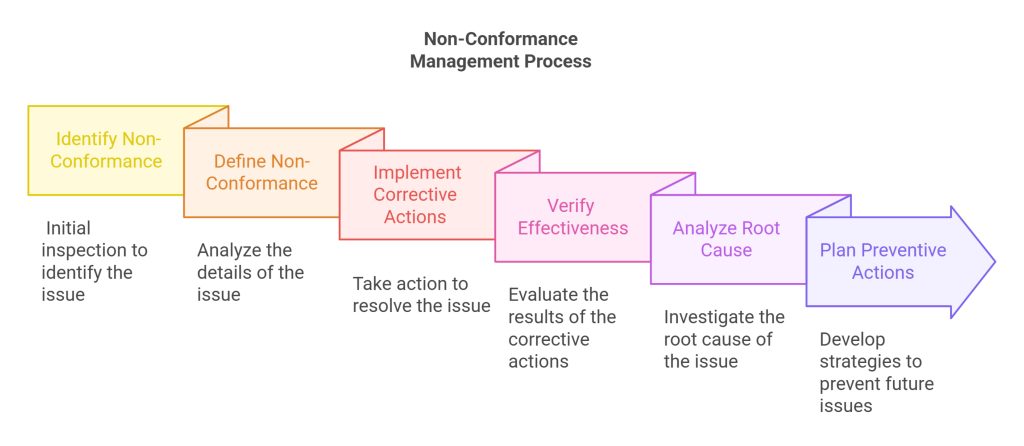
6. Stakeholder Communication
Construction quality control requires smooth communication between stakeholders. It’s important to establish mechanisms for sharing daily information by holding regular quality meetings. When important quality-related decisions are needed, it’s advisable to gather all relevant parties for discussions to achieve unified understanding.
Digital project management systems and communication tools help share information and maintain timely records.
7. Mock-ups and Sample Verification
For important finishing materials and/or special construction methods, verifying through full-scale mock-ups and samples in advance is effective. This allows stakeholders to concretely share quality levels that may be difficult to convey through drawings and specifications alone.
Additionally, mock-ups can be utilized to verify construction methods and work procedures. Particularly when dealing with complex combinations or implementing new construction methods, preliminary verification using mock-ups should be conducted.
8. QC Activities for Lifecycle Cost Optimization
Construction quality control significantly impacts building lifecycle costs (LCC). Appropriate investment in QC activities directly leads to long-term LCC reduction.
Don’t end QC and QA PDCA cycles at the construction phase. It’s essential to maintain a perspective that includes planned maintenance during the operational phase, future implementation of new technologies, and renovation plans anticipating potential upgrades. This viewpoint is crucial for maximizing the client’s asset value.
Conclusion
Effective construction quality control is crucial for project success. Professional support can help implement quality management more efficiently.
Please feel free to reach out to Plus PM Consultant, your experienced partner in construction project management, for professional consultation.
At any stage of your project, please feel free to consult with Plus PM Consultant, an experienced project management firm ready to support your needs.